Fluxograma de um processo de galvanização a fogo
Desengraxe
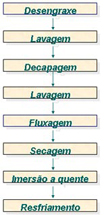
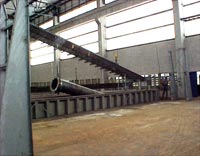
- Remoção dos materiais orgânicos, óleos e graxas;
- Processo mais conhecido: alcalino em solução aquosa a quente, à base de carbonatos, silicatos, hidróxidos, fosfatos, detergentes e outros;
- Fornecimento: normalmente no estado sólido para serem dissolvidos em água, conforme orientações dos fabricantes.
Lavagem
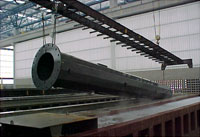
- Operação subsequente ao desengraxe;
- Operação fundamental pois qualquer resíduo que permaneça sobre a peça, contaminará os tratamentos subsequentes;
- Importante: materiais como tintas, vernizes e resinas, não podem ser removidos por banhos de desengraxe alcalino, devendo sofrer um tratamento prévio com solventes ou removedores;
- Devido às características combustíveis destes produtos, muitas vezes opta-se pela remoção por jateamento abrasivo.
Decapagem
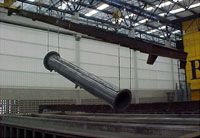
- óxidos, cascas de óxidos e carepas não são removidos nos banhos de desengraxe alcalino. Sua remoção é feita em banhos e soluções ácidas, em um processo conhecido como decapagem;
- Uma camada típica de oxidação apresenta os seguintes elementos e compostos:
- Fe (ferro base);
- FeO (óxido de ferro no estado menos oxidado);
- Fe3O4 (óxido de ferro no estado intermediário de oxidação);
- Fe2O3 (óxido de ferro no estado mais oxidado).
Características
- Camada de FeO contribui com 80% da espessura da camada total e é o elemento mais solúvel em ácidos;
- Camada de Fe3O4 contribui com cerca de 18% e é menos solúvel do que a anterior;
- A camada de Fe2O3 contribui com o restante de 2% e corresponde ao estado mais estável e menos solúvel destes óxidos.
Aspecto prático: o ácido clorídrico (muriático) é o mais comumente usado nas galvanizações brasileiras, nas concentrações de 6 a 12%.
Ataque do ácido: através das rachaduras e poros existentes na camada de oxidação, até atingir o substrato de FeO, promovendo sua dissolução e propiciando o destacamento da camada de óxido.
Quimicamente, o elemento mais solúvel nestas circunstâncias é o Fe base através da reação:
Fe + 2HCl è FeCl2 + H2
Cuidado especial: Ocorre a geração de hidrogênio nesta reação que, se por um lado auxilia mecanicamente a remoção da camada, por outro, dissolve-se no ferro base fragilizando a peça (fragilização por hidrogênio).
Utilizam-se então:
- Inibidores (reduzindo o ataque do ácido ao ferro base);
- Substâncias que promovam redução da tensão superficial entre o ácido decapante e a peça (ação umectante, facilitando seu "molhamento");
- Agitação e aquecimento aumentam a velocidade de decapagem.
Lavagem
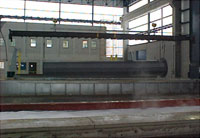
Após a decapagem é muito importante que as peças sofram uma lavagem em água corrente, em banhos subsequentes (de preferência mais de um) com a finalidade de remover os resíduos produzidos nas reações de decapagem, de forma a minimizar as contaminações dos banhos seguintes.
Fluxagem
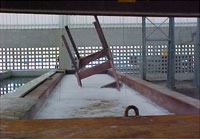
A ação do fluxante processa-se sob duas formas:
- Parte é consumida na dissolução e escorificação dos resíduos remanescentes
- O restante exerce a função umectante ( ou mordente ) proporcionando um eficiente molhamento da peça pelo zinco fundido
Principais componentes de um fluxante
- São os compostos químicos cloreto de zinco ( ZnCl2 ) e cloreto de amônio (NH4Cl), formando sais duplos;
- A grande vantagem de utilização de fluxos baseados em cloretos duplos de zinco e amônia é a redução drástica na formação de borra e a melhor qualidade do acabamento;
- Concentrações variáveis de sal duplo entre 5 a 30%, dependendo do tipo de peças tratadas, em temperaturas de 65°C a 100°C.
Secagem
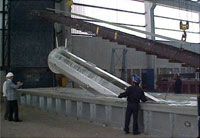
Objetivo do pré-aquecimento
- Diminuir o choque térmico das peças a serem galvanizadas;
- Prevenir contra respingos de zinco, na área ao redor da cuba de galvanização, durante a imersão da peça no zinco fundido, fato que acontece quando há umidade.
Cuidados práticos
- Início sempre imediatamente após a retirada da peça do banho de fluxo, para manter a continuidade do aquecimento já iniciado na fluxagem;
- Manter um fluxo contínuo de trabalho conforme o mix de produto;
- Manter a temperatura entre 110º e 140ºC;
- Temperaturas baixas não permitem a remoção total da umidade, havendo o risco de explosões durante o mergulho;
- Temperaturas altas, acima de 150ºC, produzem superaquecimento que decompõe o fluxo e acarreta falhas na camada zincada;
- Aconselha-se galvanizar as peças imediatamente, pois devido à absorção de umidade pelo sal, que é bastante higroscópico, as peças podem se umedecer novamente.
Imersão a quente - "Zincagem a quente"
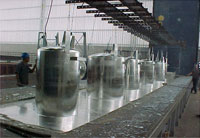
Conceito
Imersão do substrato de aço, limpo e adequadamente preparado em um banho de zinco líquido, dentro de uma cuba metálica ou cerâmica, a uma temperatura em torno de 450°C.
Explicação físico-químico-metalúrgica
- Durante a imersão, ocorre difusão do zinco no substrato de aço, havendo uma reação metalúrgica com formação de intermetálicos (compostos Fe-Zn ) cuja composição varia na espessura da camada, sendo que a porção mais externa é constituída basicamente de zinco puro;
- Para o aço baixo-carbono revestido em banho de zinco fundido, sem nenhum elemento de adição e para as condições de operação comumente utilizadas, obtém-se um revestimento constituído por quatro fases.
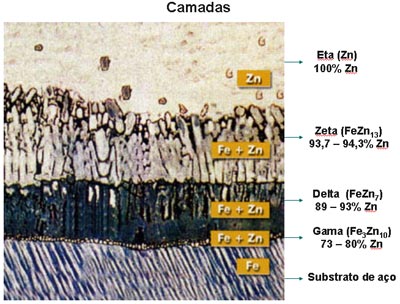
Características principais
- As três primeiras fases são formadas devido à reação entre o zinco fundido e o aço, chamadas de fases intermediárias;
- Esta reação pode continuar após a retirada do aço de dentro da cuba, se a velocidade de resfriamento for baixa;
- A última fase, denominada Eta (de zinco puro) é formada pela solidificação do zinco fundido aderido à peça por arraste.
Aspectos importantes na Galvanização a Fogo
1. Temperatura do processo
As temperaturas usadas para zincagem variam normalmente entre 445º a 455°C.
Cuidados práticos
- Deve-se galvanizar à mínima temperatura que permita um escorrimento fácil do excesso de zinco durante a extração do material;
- Temperaturas acima de 470°C são desaconselháveis pois a reação do zinco com as paredes da cuba (para o caso de cubas metálicas) se torna muito intensa acelerando seu desgaste e diminuindo sua vida útil;
2. Velocidade de imersão e remoção
Velocidade de imersão
- A imersão deve ser a mais rápida possível para que não haja tempo de uma espessa camada de zinco se formar na primeira parte da peça, antes que toda ela tenha entrado em contato com o zinco;
- A velocidade de imersão varia de 6 a 7 m/minuto.
Velocidade de remoção
- Em contrapartida, quanto mais lenta e constante for a velocidade de remoção, melhor será a uniformidade da camada e menos espessa a camada "eta";
- A velocidade de remoção está na média de 1,5 m/minuto.
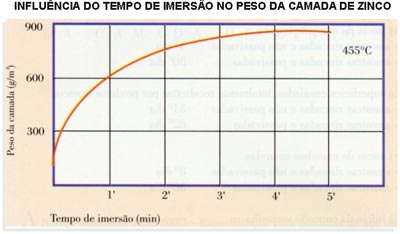
3. Tempo de imersão
- Quanto maior o tempo de imersão, mais espessa é a camada, até determinado limite, passando a ocorrer uma estabilidade;
- Observa-se um crescimento acentuado no primeiro minuto de imersão, etapa que corresponde à rapidez da reação entre o zinco e o ferro para, em seguida, ocorrer uma etapa de reação mais lenta, correspondendo a um consequente crescimento mais lento da camada.
Aspecto prático
- O término da primeira fase, na prática, é percebido durante a zincagem pelo cessar do borbulhamento da superfície do banho. Para espessuras normais de camadas, este fenômeno é uma indicação do fim de reação e do momento de retirada da peça do banho;
- O tempo de imersão pode variar de 10 a 300 segundos.
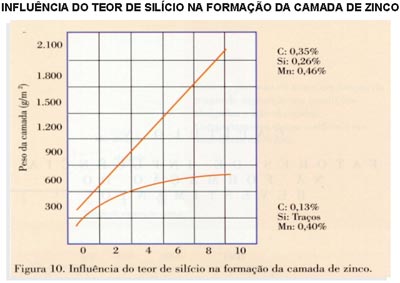
4. Composição do material base a ser galvanizado
(aço/ferro fundido)
Fator dos mais importantes na formação e evolução da camada zincada
- Elementos que mais ativam a reação entre o zinco e o aço a ser galvanizado: carbono, silício, fósforo, enxofre e manganês (C-Si-P-S-Mn);
- Mais reativo e mais comum de aparecer entre eles: silício (Si);
- Acima de 0,12% o mecanismo normal de formação da camada Fe-Zn é modificado, obtendo-se camadas espessas e de coloração escura acinzentada.
5. Composição do banho de zinco
- O zinco utilizado nas galvanizações brasileiras é o Zn SHG (Special High Grade) com pureza igual a 99,995%;
- O metal mais utilizado como elemento de liga do banho de galvanização é o alumínio. é adicionado em pequenas quantidades, de forma a se ter no banho de galvanização em média cerca de 0,0050%;
- Aconselha-se ter no banho no máximo cerca de 0,01%. Acima deste teor podem ocorrer vários tipos de problemas nas peças galvanizadas além de reagir com o aço da cuba metálica;
- A finalidade de se adicionar Al no banho é a de promover melhor escorrimento, melhor uniformidade das camadas e maior brilho das peças recém galvanizadas.
Resfriamento
- Aconselha-se um resfriamento rápido em água, para que cesse o crescimento das camadas de ligas, evitando-se uma cristalização grosseira e frágil.
Aspectos práticos
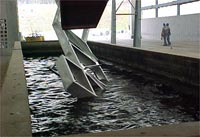
- Em algumas galvanizações, aproveita-se este tanque de resfriamento para realizar a passivação da camada de zinco das peças galvanizadas;
- Trata-se de um banho rápido em soluções cromatizantes, à base de ácido crômico e bicromato de sódio, com a finalidade de retardar o aparecimento da chamada "corrosão branca" (capa protetora em torno de 0,5µm de cromato de zinco insolúvel);
- Esta passivação confere ao zincado um aspecto ligeiramente amarelado, sendo mais claro quanto menor a concentração da solução ou menor o tempo de imersão.
Aspecto prático: Coloração da peça X Corrosão
- Corrosão branca: é característica da corrosão do zinco. Inicia-se quando a proteção da passivação foi comprometida;
- Corrosão vermelha: coloração típica quando a corrosão atinge o metal base.
Estocagem dos materiais galvanizados.
Orientações gerais
- Resfriamento em solução cromatizante;
- Empilhar as peças somente quando secas;
- Adotar o critério de, sempre que possível, empilhar as peças com qualquer parte côncava para baixo;
- Passar a fita de aço para fixar os amarrados, sobre uma faixa de estopa para proteger o galvanizado;
- Empilhar os amarrados, um sobre o outro, com espaçadores de madeira, não esquecendo que o primeiro, rente ao chão, deverá estar também sobre estes espaçadores.
Resíduos gerados no processo de galvanização a fogo
Borra de Zinco
- Borra de zinco, mais conhecida como "areião", é um resíduo formado por cerca de 96% Zn e 4% Fe;
- Aparência arenosa e composta de cristais de ferro-zinco insolúveis à temperatura normal de trabalho, que se depositam no fundo da cuba durante o processo de galvanização;
- Além de representar uma perda de zinco, prejudica o aquecimento da cuba, (mau condutor de calor) e o aspecto das peças zincadas, quando adere a sua superfície;
- Não é possível impedir a formação de borra, porém, é indispensável que se saiba sua origem para poder controlar sua formação.
Cinza de Zinco
- Cinza de zinco, mais conhecida como "terra de zinco", é um resíduo composto de óxido de zinco, zinco metálico e cloretos em teores variáveis;
- A cinza forma-se na superfície do banho devido à oxidação do zinco com o oxigênio do ar e as escórias da reação fluxo-zinco-ferro.
Pó de zinco
- Pó de zinco – existe exaustor sobre o banho de zincagem que faz a extração do óxido de zinco em suspensão, arrastado para o filtro manga, depositado finalmente em reservatório apropriado.
Facilitadores na geração de cinza
- Temperatura de trabalho, quanto mais alta, mais intensa a oxidação da superfície do banho;
- Agitação do banho, quanto maior a perturbação da superfície do banho, mais intensa é a formação de cinzas.
Saiba mais sobre estudos de casos »
Voltar